As the world moves into Industry 4.0, businesses are looking for new ways to harness the power of digital technology to create efficiencies and improve their bottom line. But what is Industry 4.0, and how can your business benefit? In this blog post, we’ll explore those questions and more, so you can be at the forefront of this latest industrial revolution.
The ever-increasing rate of product obsolescence is putting pressure on manufacturers to change how they operate. In the past, a product would have a shelf life of three to five years before it became outdated. Nowadays, that timeframe has shrunk to just 14 to 18 months. This shorter lifespan necessitates a different approach to Manufacturing, which emphasizes customization, quality, and performance more.
We are now entering what is described as a fourth revolution, also known as Industry 4.0. It is the next phase in the evolution of Manufacturing. While Industry 4.0 is often spoken about in terms of its potential to modernize Manufacturing and boost industrial competitiveness, its benefits extend well beyond that. Industry 4.0, coupled with the Internet of Things (IoT) and Digital Twins, offers business owners the ability to collect, analyze, and act on data like never before. This data can be used to improve the quality of products, lower operating expenses, and increase efficiency. In addition, automated robotics allows businesses to set these improvements in motion quickly and efficiently. As a result, Industry 4.0 is transforming Manufacturing and revolutionizing the way companies operate.
What is Industry 4.0?
Industry 4.0 is the term used to describe the fourth industrial revolution. This revolution is characterized by a shift from traditional Manufacturing to a more digitized and connected form of Manufacturing. It is a transformation driven by the convergence of physical and digital technologies. It includes cyber-physical systems, the internet of things, cloud computing, and cognitive computing. Industry 4.0 is enabled by a digital manufacturing ecosystem that is connected, data-driven, and automated. This ecosystem comprises smart factories, supply chains, products, and services. It enables a new level of interconnectivity and collaboration between people, machines, devices, and systems.
This digital manufacturing ecosystem has the potential to increase productivity, flexibility, and efficiency dramatically. It also can create new business models and value propositions. Industry 4.0 is still in its early stages but holds great promise for the future of Manufacturing. Additionally, Industry 4.0 uses advanced technologies such as 3D printing and robotics. These technologies allow for more personalized and custom products to be produced on a mass scale. As a result, Industry 4.0 represents a significant shift in how goods are produced and consumed.
In Industry 4.0, factories can communicate and share data in real-time. This allows for more responsive and agile manufacturing processes. Coupled with the IoT, Industry 4.0 allows manufacturers to collect, analyze, and act on immense stockpiles of data like never before and then set those actions in motion with highly efficient, automated robotics. The result for business owners? A higher-quality product at a lower operating expense. In addition to increased efficiency and productivity, Industry 4.0 offers better insight into customers, processes, and business models. By helping companies move away from traditional vertical integration and shift to more customer-centric and agile processes composed of modular parts that can be quickly rearranged or replaced. This increased flexibility enables companies to respond more rapidly to changing market demands.
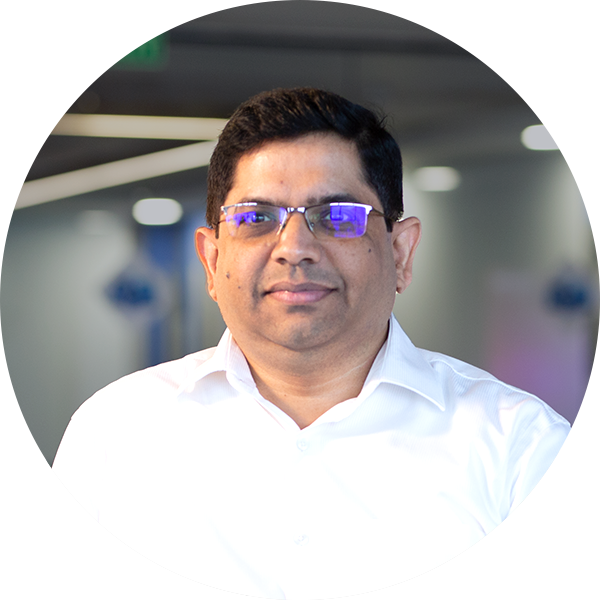
Industry 4.0 holds great promise for the future of Manufacturing. This digital manufacturing ecosystem has the potential to dramatically increase productivity, flexibility, and efficiency, thus helping create new business models and greater value.
– Hitendra Munjampally Associate Director, Microsoft MOURI Tech
Benefits of Adopting an Industry 4.0
Industry 4.0 includes several new technologies often touted for their ability to increase productivity, improve quality, and reduce costs. Here are five of the most significant advantages of adopting Industry 4.0:
- Increased Productivity: One of the main goals of Industry 4.0 is to increase productivity through automation. By automating tasks traditionally done by human workers, factories can produce more goods in a shorter amount of time.
- Improved Quality: In addition to increasing productivity, Industry 4.0 can also improve the quality of products. Automated systems can more accurately follow instructions and tolerances than human workers. As a result, factories can produce higher-quality goods with fewer defects.
- Reduced Costs: By automating production processes, factories can reduce labor costs. In addition, the increased accuracy of automated systems can lead to reduced material waste, further reducing costs.
- Flexibility: Another advantage of Industry 4.0 is its flexibility. Unlike traditional manufacturing processes, which are often inflexible and difficult to change, Industry 4.0 technologies can be quickly reconfigured to meet changing customer demands.
- Improved Safety: Automated systems can also improve safety in factories by reducing the need for human workers to perform tasks that could be dangerous. In addition, these systems can help to identify potential safety risks before they occur, further reducing the likelihood of accidents or injuries.
Industry 4.0 – The Challenges
The fourth industrial revolution, which is the current trend of automating manufacturing processes, is a significant upgrade from yester years when companies relied heavily on manual labor. Industry 4.0 involves advances in digital technology that transform Manufacturing and the industrial sector. Factories can now produce more goods at a lower cost and with less waste. However, there are a few challenges associated with this new era of Manufacturing. One challenge is it requires a high level of investment in both hardware and software. In addition, finding workers with the necessary skills to operate the new technology can take time and effort. Also, today’s organizations rely heavily on data collection and analysis and this data must be managed securely to protect intellectual property and avoid cyberattacks.
The Way Forward
Despite these challenges, Industry 4.0 has the potential to revolutionize Manufacturing and create a more efficient and sustainable industrial sector.
MOURI Tech provides flexible, industry-specific software solutions to help you implement Industry 4.0 technology into your business. Our solutions are designed around the needs of Manufacturing, Distribution, Retail, and Service Industry customers.
Author Bio:
Hitendra Munjampally
Associate Director, Microsoft
Hitendra has a strong track record of leading and enabling teams to deliver cutting-edge IT solutions to enterprise customers across Hi-Tech, Manufacturing & Health, Energy & Utilities, Travel & Logistics and Services industry domains. He has extensive experience in developing IT strategy, next-gen service offerings, pre-sales, technology solutions & accelerators to help customers digitalize and modernize their workloads, leveraging Microsoft capabilities.